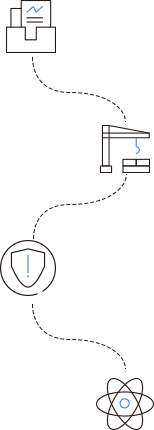
石油生产的连续性生产要求,对石油装备的非计划停机提出了非常高的要求,需要通过各种实时监控、定期的计划性维修和不定期的视情维修,对设备进行有效的维护,避免由于设备的无计划停机造成巨大的损失。
建设投资巨大
对于设备运营商,在故障维修模式上,由于缺少有效的设备状态数据采集、数据存储、分析和寿命预测手段,在关键设备的维护上往往无法在过度维修(定期巡检)和被动维修(故障停机之后的维修)之间取得有效的统一。
安全风险
一方面,对于可遇见的易损部件可以通过定期的保养,对部件进行及早更换,但带来的却是维护成本、备品备件的管理成本居高不下;另一方面,对于无法预计的一些状态,可以采用基于振动分析和状态监测的手段,根据检测结果来优化维修策略,但往往只能实现固定场景下的有限的故障预测,无法覆盖到更广的范围。
业务创新困难
这种维护模式虽然能够在一定程度上保证设备的可靠性,但客户不得不去安排更多的人力、预留更多的备品备件来配合,因此带来的维修成本往往是非常高的。